Matt Krug
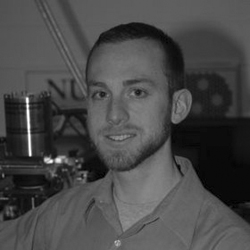
- Ph.D. Student (alumnus)
- Aluminum-Scandium Alloys
- Email: m-krug(@northwestern.edu)
- Address: 2220 Campus Drive, Evanston, IL 60208
- B.S., Carnegie Mellon University;
Master de Recherche (M2),
Ecole Centrale de Paris
If you’re reading this page on your PC, drove your car (or better yet, rode your bike) home from work today, flicked on a light recently, or popped open a can of soda, you’ve benefited from advances in materials science. That’s what is so fascinating about it: materials are everywhere, and from quantum physics to fracture mechanics, there are a lot of tools at a materials scientist’s disposal when trying to describe the natural world. That’s what got me interested in this field.
I grew up in Altoona, Pennsylvania and got my B.S. in materials science at Carnegie Mellon University in Pittsburgh. Afterwards, I worked for three years at Westinghouse Electric Corporation (also in Pittsburgh) in the Materials Reliability department. My primary responsibilities were related to nuclear reactor core internals, and primary coolant pump seals. With regard to the internals, I was engaged in several programs which involved measuring the mechanical properties of irradiated type 304 stainless steel. The pump seal work involved accelerated hydrothermal corrosion testing of silicon nitride in order to assess the useful lifetime of the pump seals. Pumping 100,000 gallons per minute of coolant at 2500 psi is tricky business. I then left Westinghouse to continue my education at the École Centrale de Paris near Paris France, where I recently got my masters degree. It was a hard year, but strolling through the market in my little adopted town of Draveil, walking the streets of Paris, and watching the world cup mania unfold in person, made it worth the effort.
I’m currently in the PhD materials science program at Northwestern University where I am coadvised by Professors Seidman and Dunand. My thesis project involves casting, testing, and characterization of aluminum-based alloys for high temperature applications. Small additions of Scandium and certain rare-earth elements to Aluminum, with an appropriate heat treatment, result in a very fine dispersion of ?’ precipitates which serve to strengthen, impede grain growth, and impart high-temperature creep resistance to the alloy. It is possible that additions can further increase the creep resistance of the alloy, and this will be my focus in the early stages of my work. The very small (nanometric) size of the precipitates will necessitate the use of transmission electron microscopy, as well as three-dimensional atom probe tomography to characterize the alloys throughout their heat treatment. With a thorough understanding of these effects, light-weight Aluminum alloys may one day be an attractive candidate for engine applications, where efficiency improvements depend in part on increasing the operating temperature.