With increasing needs for energy saving and emission reduction, Co-based superalloys can provide higher operation temperatures which allows for higher efficiency of gas turbines for electric generation and jet engines for aviation. Additively-manufactured Co-based superalloys offer unique opportunities for overcoming challenges of poor machinability and limitations of casting for complex, thin-walled geometries.
We are demonstrating a blended elemental route for Co-based superalloys to help develop future high-throughput studies using additive manufacturing. We aim to create Co-based superalloys via additive manufacturing with homogeneous γ' (L12)/γ (FCC) microstructure and excellent mechanical performance based on alloy composition predictions by NIST. We focus on microstructural characteristics upon laser melting and heat treatment process, based on understanding of metal dissolution and mixing kinetics in the melt pool and precipitation kinetics. We therefore aim to tailor additive manufacturing process and investigate the effects of the elements on microstructure of Co-based superalloys as well as mechanical properties.
We are also studying processing-related microstructural defects formed during laser melting, i. e., cracking, incomplete fusion or dissolution. Finally, we study the alloy's hardness (at ambient temperature) and creep resistance (at 800 C), based on their microstructures.
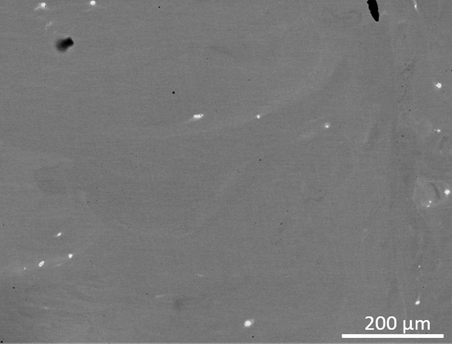
SEM micrograph of Co-Ni-Al-W superalloys fabricated by selective laser melting of an elemental powder blend, showing low number density of pores (black) and incomplete dissolution of tungsten powders (white).
Related Publications
Funding support
- CHiMaD: Center for Hierarchical Materials Design